I thought that the process of creating familiar ceramic tiles was very familiar to me. However, a recent trip to the Kerama Marazzi factory in the village of Malino near Moscow added to my understanding of the company and the production process itself. From the very first minutes on the factory premises you can feel a special atmosphere: the industrial landscape is unexpectedly combined with art. On the facade of the main building shines a monumental mosaic “Factory” - a whole picture the size of a house, created by contemporary artist Anton Chumak. This bright art-object immediately attracts the eye and makes us realize that not an ordinary excursion awaits us, but a journey into the very soul of production.
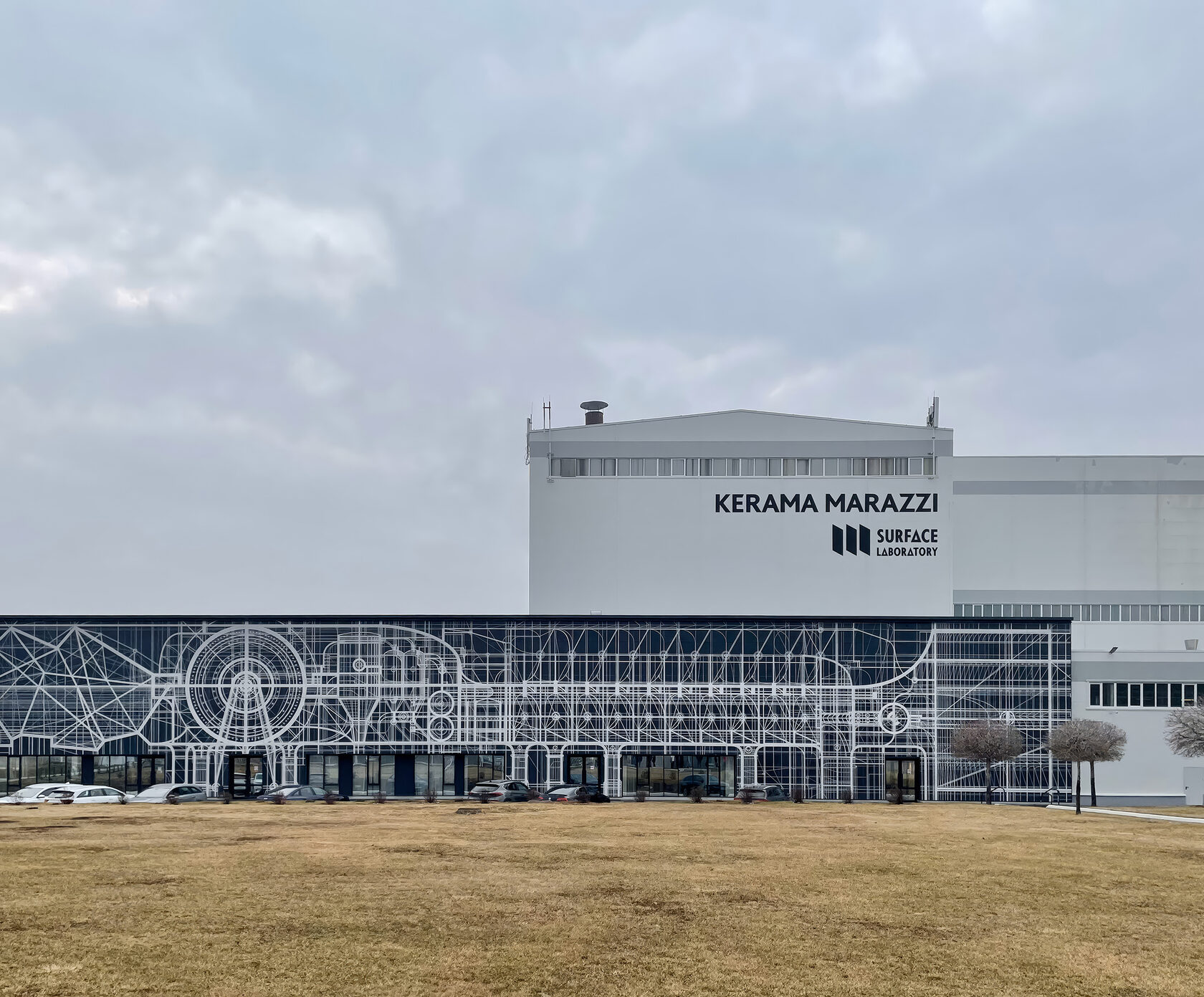
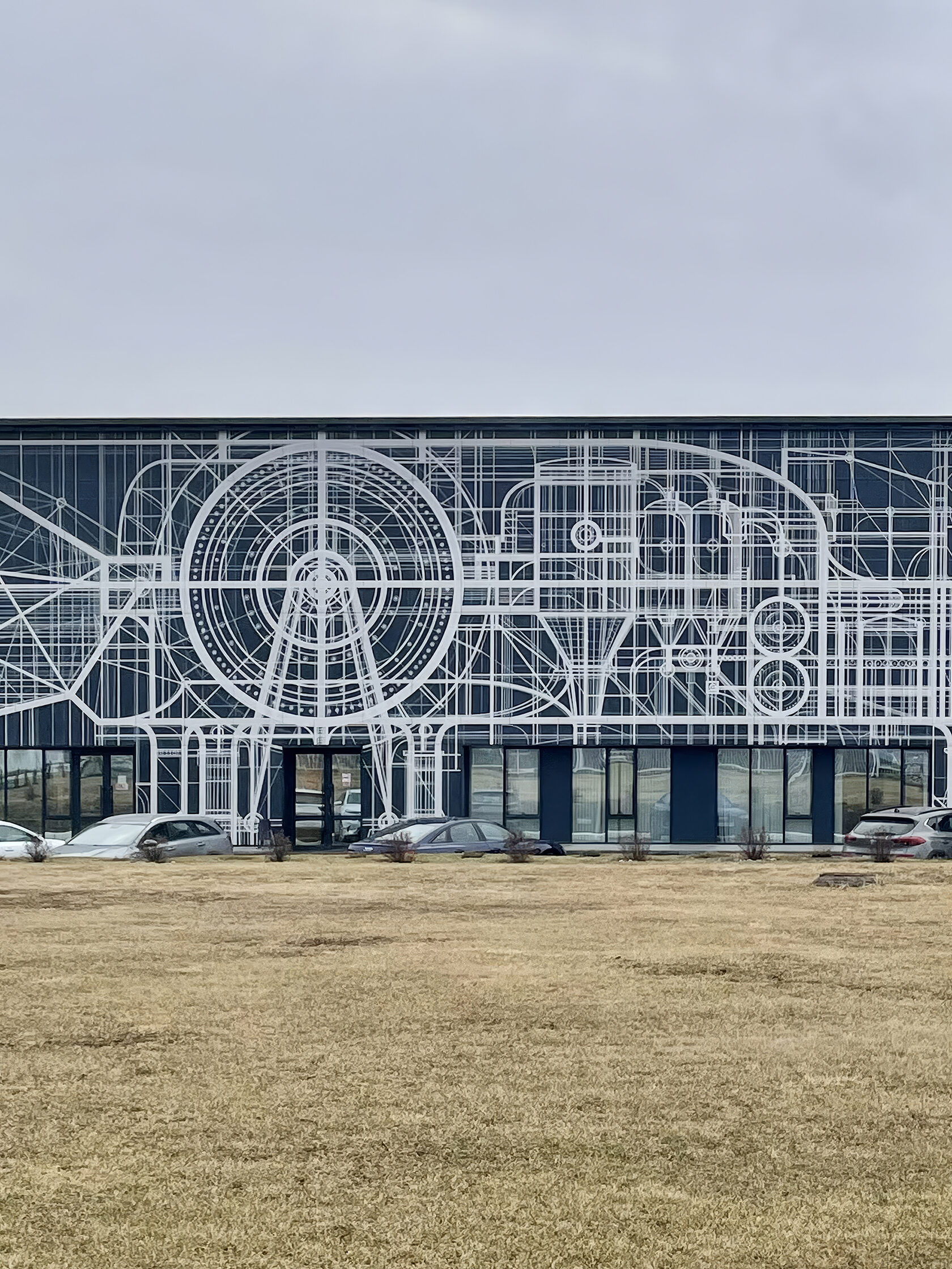
The first meeting: a factory that surprises you from the doorstep
Instead of dull gray walls we were greeted by a modern architectural complex and the very bright facade with mosaics - the plant literally put on a work of art as a bold outfit. A warm welcome awaited the guests at the entrance hall: despite the safety rules, we could feel the sincere hospitality and pride of the employees for their brainchild. Already at this stage, I noticed how clean and well organized the place was. I have been to different production facilities, including European ones, and I have something to compare with. And for myself I noted the modernity, cleanliness and scale of the enterprise.
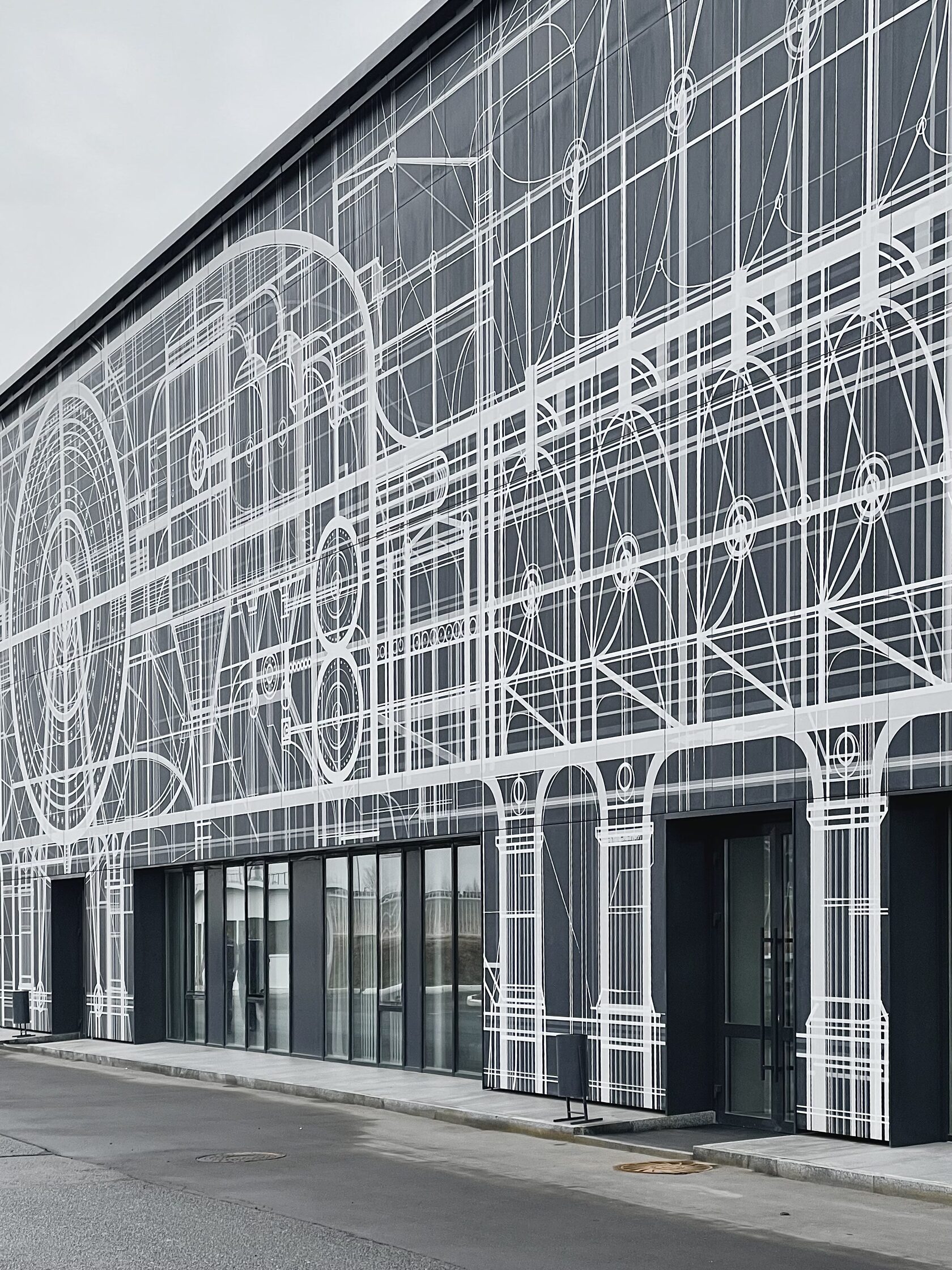
How the tiles are born: a tour of the production site
After listening to the safety instructions, wearing signal vests and audio headset, we go to the heart of the production. The tour starts where the tiles themselves originate - in the raw material preparation area. Under a huge canopy we can see mountains of sand, clay and minerals. In front of us - the very “chaos” from which porcelain stoneware is born, as Anton Chumak aptly noted. But go a little further, and the chaos turns into an orderly process: raw materials are dosed into mills, where they are ground into the finest powder and then thoroughly mixed according to the recipe. This powder - the future “dough” for the tiles - is fed to the molding area.
Next we are treated to a real machine show. Giant presses are lined up in the molding shop - steel giants that compress the powder with the force of hundreds of tons, giving birth to the base of the tiles. Each blank is cut out clearly, like a cookie with a mold. Next to the plant's pride - the newest Continua+ line, which looks more like a futuristic conveyor belt than a traditional press. It allows to produce porcelain stoneware slabs of extra large format - up to 160×320 cm. It is mesmerizing to watch it work: the belt moves continuously, forming a wide web of press powder, which is then cut into slabs of the required size.
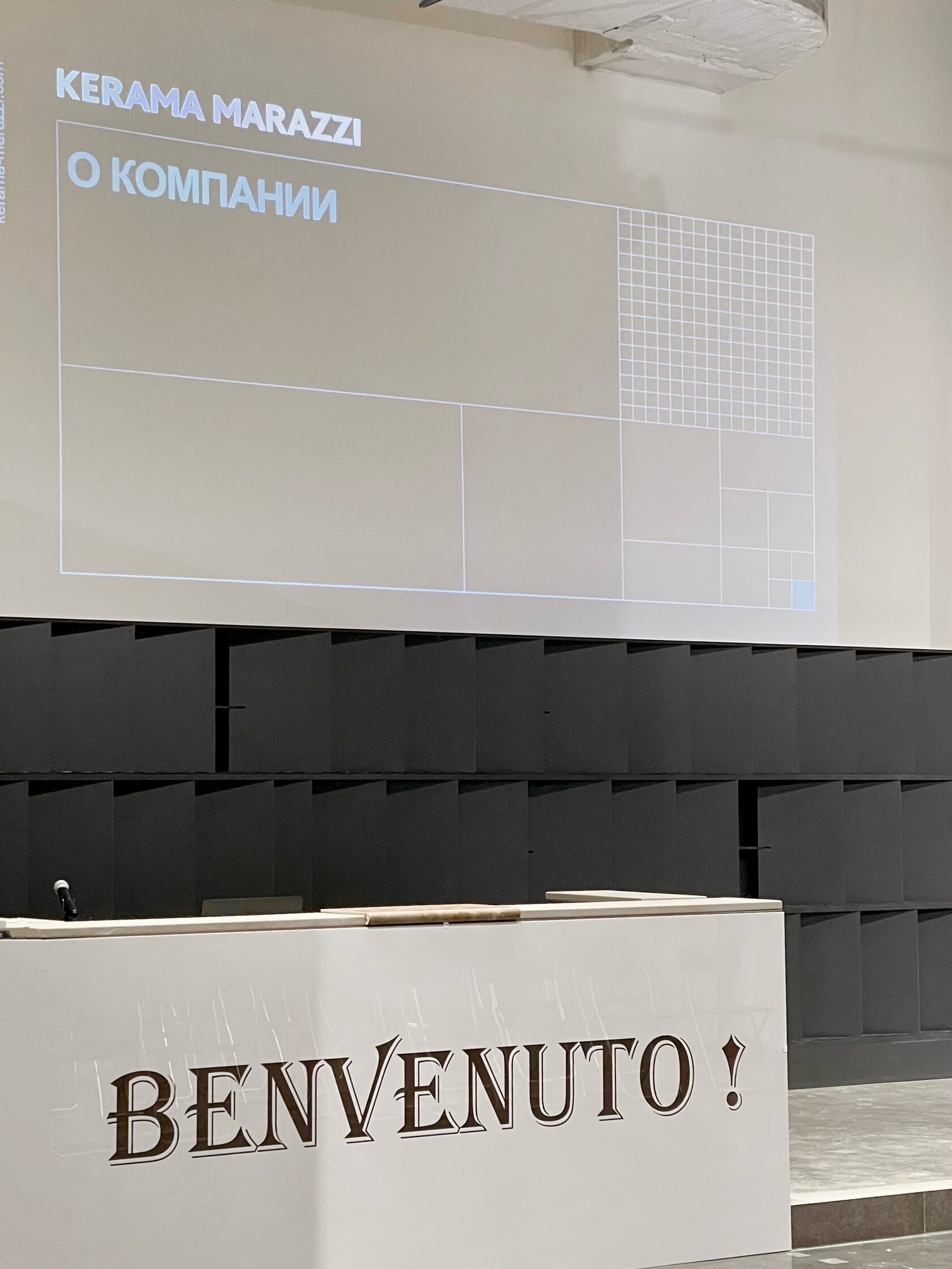
After forming, the tiles are carefully sent for drying and then for firing. We peer into one of the long tunnel kilns, the length of which seems endless. In the heated interior of the kiln, at a temperature of around 1200 °C, the brittle raw material turns into stone - porcelain stoneware acquires its legendary strength. It is like watching nature accelerate the creation of a mineral: instead of millions of years of geological processes, it takes a few tens of minutes in the fiery furnace. At the end of the process, robotic mechanisms gently take the fired tiles and send them for gradual cooling.
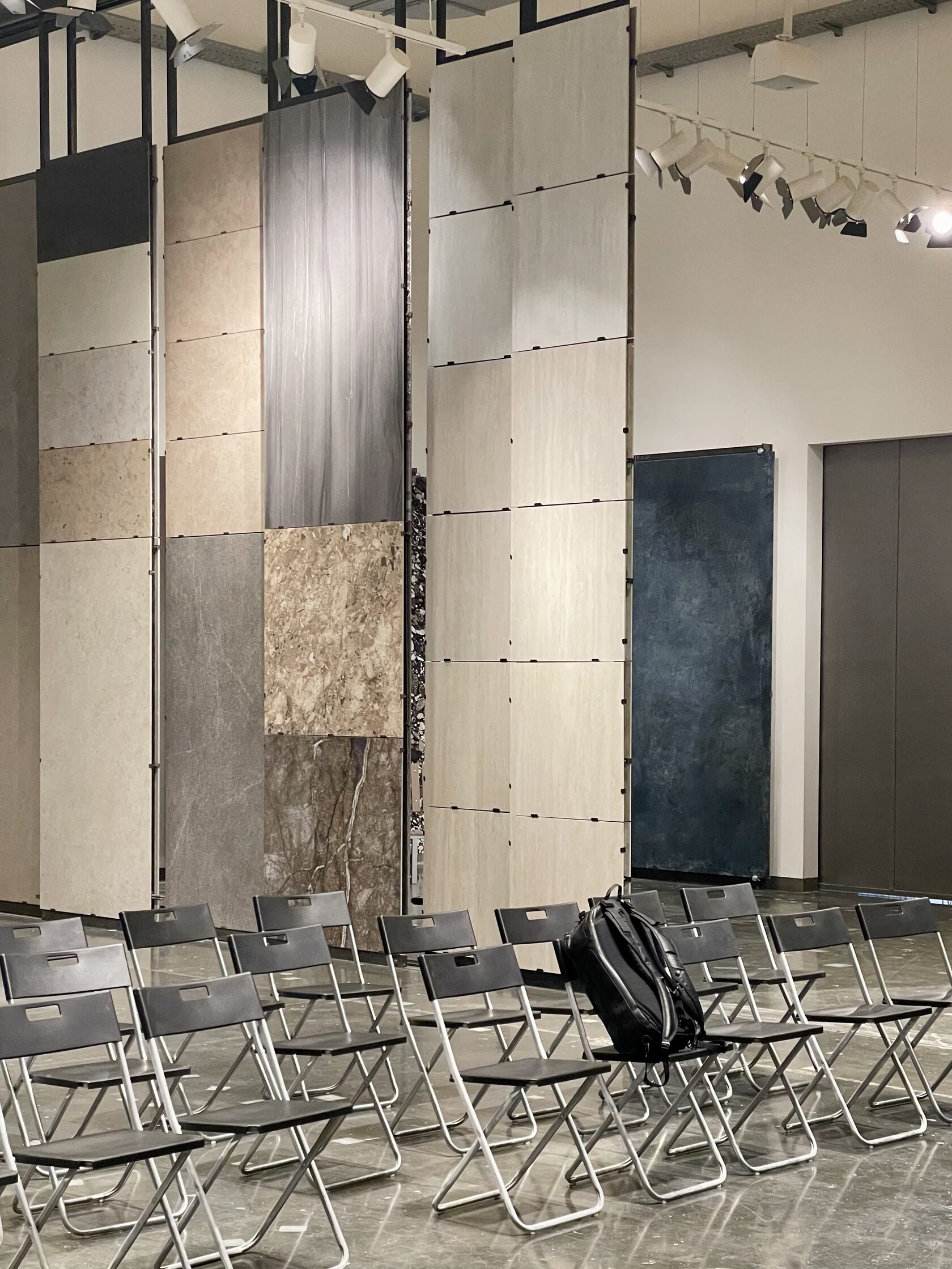
Then comes the turn of quality control and final finishing. Each tile passes through an automated sorting system: lasers and cameras check the geometry and surface, rejecting the smallest defects. If necessary, the products are refined - for example, polished to a soft shine (lappatized) or the edges are neatly trimmed. Thanks to this precise calibration, the tiles acquire a perfect geometry, which allows them to be laid almost seamlessly. We see the finished product batches stacked neatly on pallets. Automatic forklifts pick up these pallets and take them to the huge warehouse. It's like a library where, instead of books, there are volumes of samples of all the different textures and formats of tiles.
Technology and innovation: the factory of the future in the present
Even during the tour it becomes obvious: we are not just a factory, but a world-class high-tech production facility. The enterprise is equipped with equipment from leading Italian companies - not every European factory can boast of this. It is no coincidence that factories Kerama Marazzi is considered one of the most modern in Europe. Automation of processes is impressive: conveyors, robotic manipulators and digital control systems work harmoniously, as if performing a pre-rehearsed ballet. Man is the conductor of this symphony of machines - engineers watch a multitude of screens, controlling temperature, pressure, colors and dozens of other parameters.
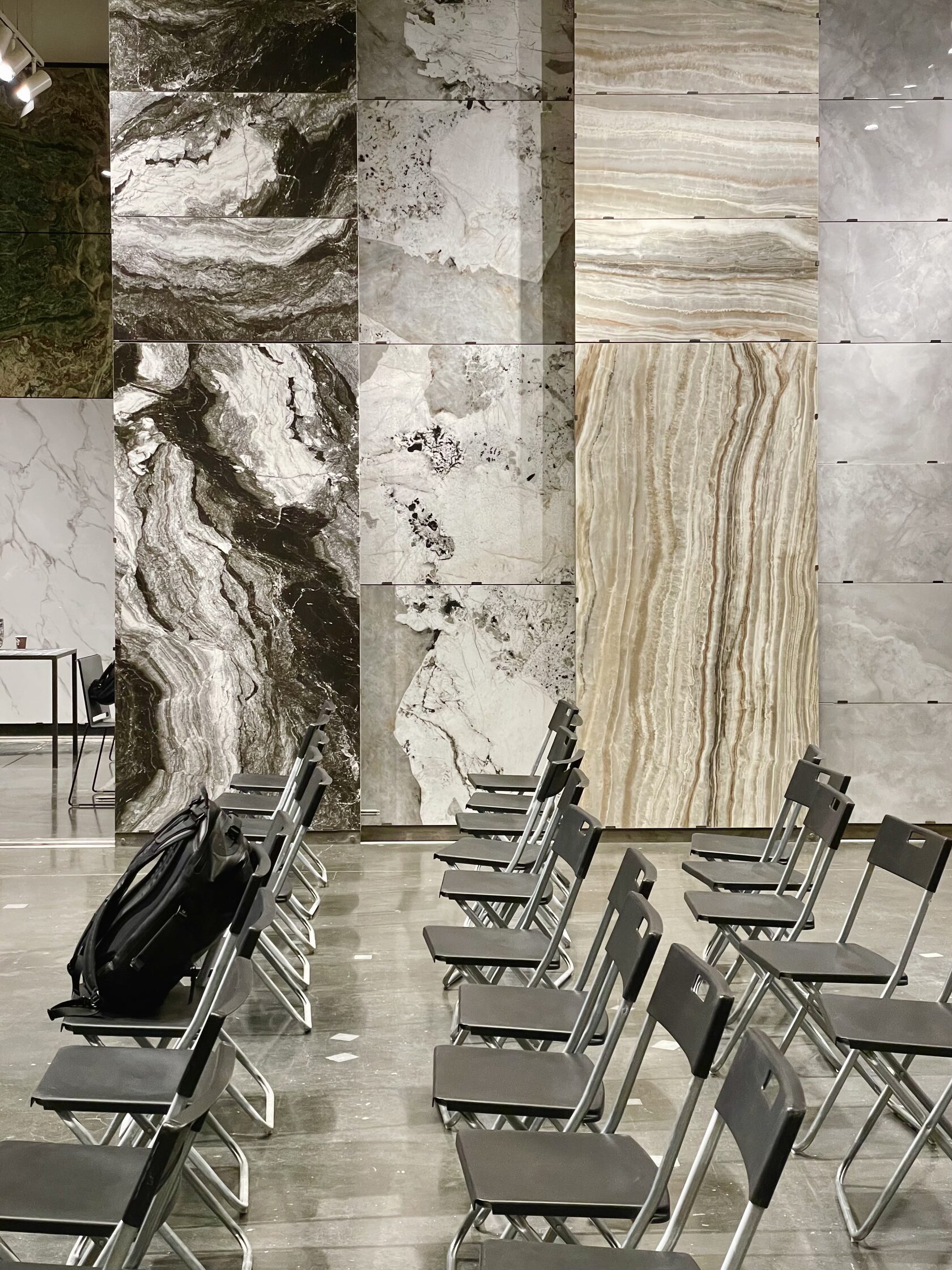
Impressive and the scale of production: the total plants Kerama Marazzi produce about 38 million square meters of tiles per year. But at such volumes, attention to quality and design is not lost. The company invests not only in machinery, but also in creativity: the development of new collections are working on famous Italian design studios, bringing current ideas and aesthetics. Thanks to modern technologies it is now possible to transfer almost any pattern or texture onto porcelain stoneware. We were shown samples of tiles indistinguishable from marble, wooden boards and even canvas with watercolors - indeed, you can embody anything on ceramic, whether it is the structure of concrete or author's graphics.
The unique technological methods used at the factory deserve special attention. For example, here is mastered the method of dry coloring of the mixture: pigments are added directly to the press powder, so that the color and pattern permeate the entire thickness of the tile, not just its surface. This makes the texture deeper and the coloring more resistant to wear and tear. Constant introduction of such innovations is part of the company's philosophy. Not without reason Kerama Marazzi was the first manufacturer of ceramic materials in Russia to receive the international Environmental Product Declaration (EPD). This document confirms that at all stages - from raw material extraction to utilization - the environmental impact of products is minimal. The latest technologies are not only for beauty, but also for sustainable development.
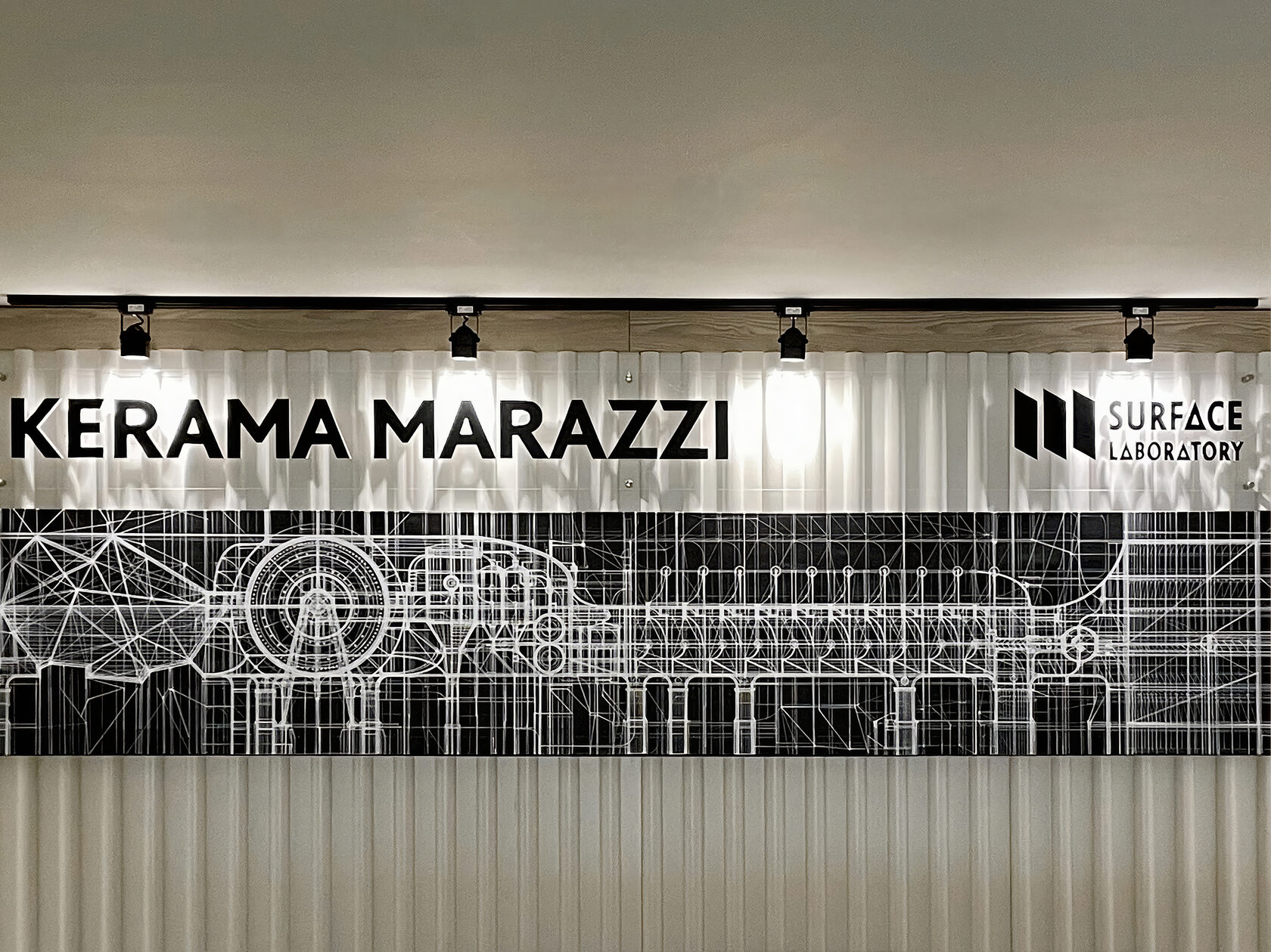
Monumental mosaic “Factory”: the factory speaks the language of art
During the trip we had the feeling that the plant in Malino is not only about technology, but also about creativity. And the best proof is the mosaic “Fabrika” on the facade. This art object was opened at the end of 2024 as a joint project between Kerama Marazzi and the creative Surface Laboratory. The idea of decorating an industrial building with a work of art continues the tradition of Soviet monumental art, when factory facades were often decorated with mosaics and bas-reliefs. However, the content of the new work is completely modern: if in the era of socialist realism on the walls glorified the heroes of labor and industrial progress, here the central “hero” is the production process itself - the transformation of natural materials into porcelain stoneware slabs.
Anton Chumak's canvas is really devoted to the alchemy of tile creation. The artist in an abstract, surrealistic manner showed the path from spontaneous natural chaos to the ideal order of industrial products. In the center of the composition - the image of transformation, where from the multicolored mass gradually draw out the correct squares of tiles. “As a child, the factory seemed to me a magical and sacred place... When you see piles of sand and clay, it is a kind of chaos. Through production, all this mass is transformed into structured pallets with even, precisely counted slabs...”, - says the author of the panel . These words perfectly reflect both the idea of the mosaic and what we observed on the tour with our own eyes.
Anton Chumak's canvas is really devoted to the alchemy of tile creation. The artist in an abstract, surrealistic manner showed the path from spontaneous natural chaos to the ideal order of industrial products. In the center of the composition - the image of transformation, where from the multicolored mass gradually draw out the correct squares of tiles. “As a child, the factory seemed to me a magical and sacred place... When you see piles of sand and clay, it is a kind of chaos. Through production, all this mass is transformed into structured pallets with even, precisely counted slabs...”, - says the author of the panel . These words perfectly reflect both the idea of the mosaic and what we observed on the tour with our own eyes.
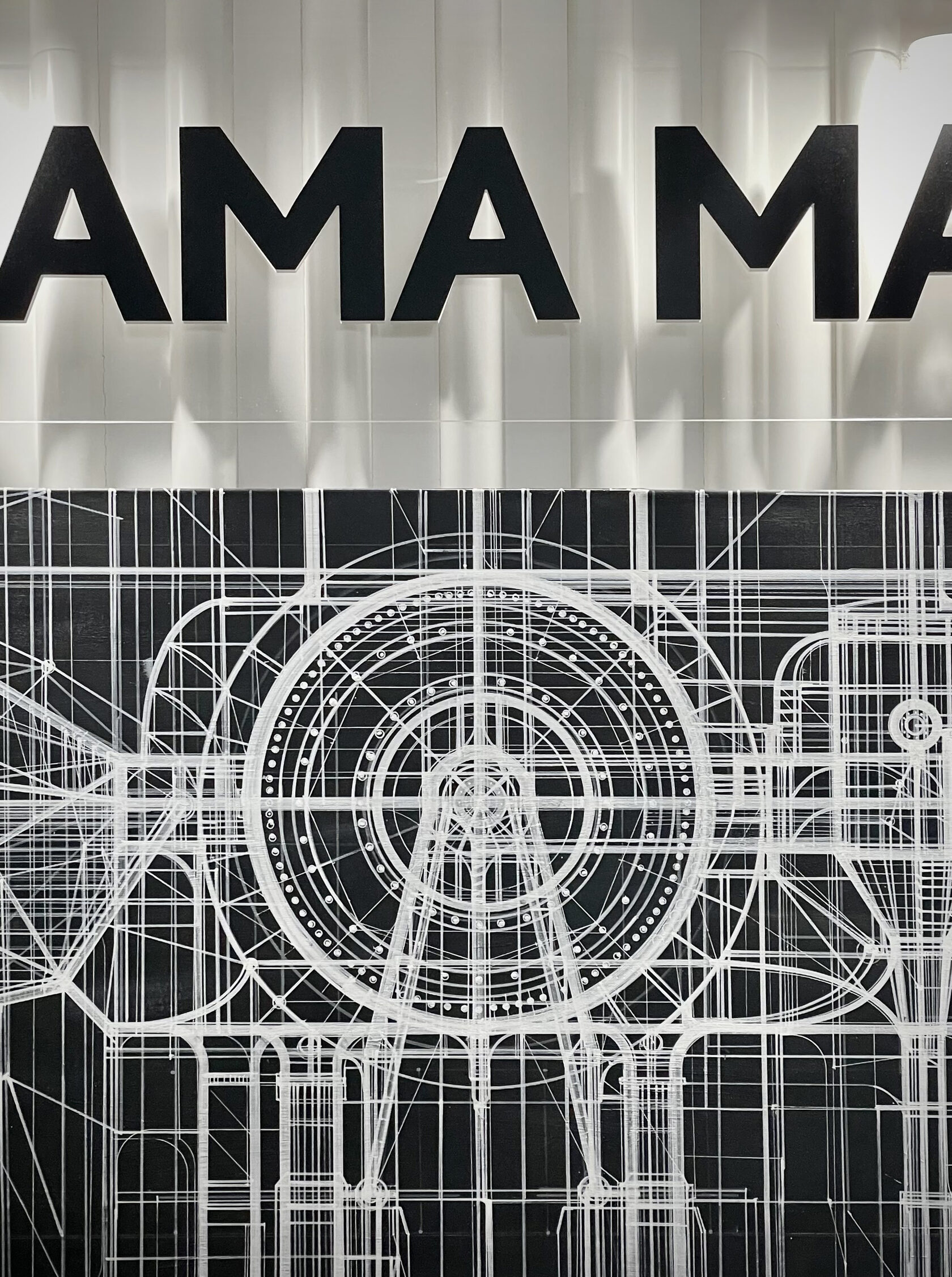
Not only the idea, but also the technology of realization of this work is unique. In fact, the “Factory” is not a classic mosaic of smalt, but a printed image transferred to ceramic panels of 320×120 cm format. There are about 200 such panels, and together they form a giant panel of 642 m², which decorates the facade. It turns out that the factory has decorated itself with its own product - porcelain stoneware - turning it into art. All the innovations mentioned above were used to create the panel: high-resolution digital printing and large-format slabs produced by the Continua+ line. The result is impressive not only for its artistic intent, but also for its durability. The porcelain stoneware panels withstand both frost and heat, keeping the colors rich and bright. The facade has actually become an open-air museum, free and accessible to all.
And the main thing is that this panel contains the philosophy of the plant. As noted by the creators themselves, the goal of the project was to connect the external appearance of the factory with its internal content. And indeed, looking at the “Factory”, any visitor from the threshold understands what is going on inside: the chaos extracted from the ground is transformed here into beauty and order. The factory seems to speak to the viewer in the language of art, demonstrating its essence. This integration of creativity into the industrial environment is not only pleasing to the eye, but also enriches the space around it. The industrial building is no longer alien: Kerama Marazzi's facade is now harmoniously integrated into the surrounding landscape and provides inspiration for employees and local residents. Seeing this example, one begins to believe that the future of industrial areas lies in creative collaborations like this, which can turn factories into landmarks.
Inspiration for new projects
Leaving the hospitable factory in Malino, I catch myself thinking that I return not only with a baggage of new ideas for current and future projects. This trip reminded me that architecture and design, and most importantly, the demand for their high quality, is one of the catalysts of production progress. Here - in the workshops, where technology and creativity go hand in hand, it is clearly visible.